A B O U T U S
Our Mission is Simple. We Make Life Easy for Our Clients
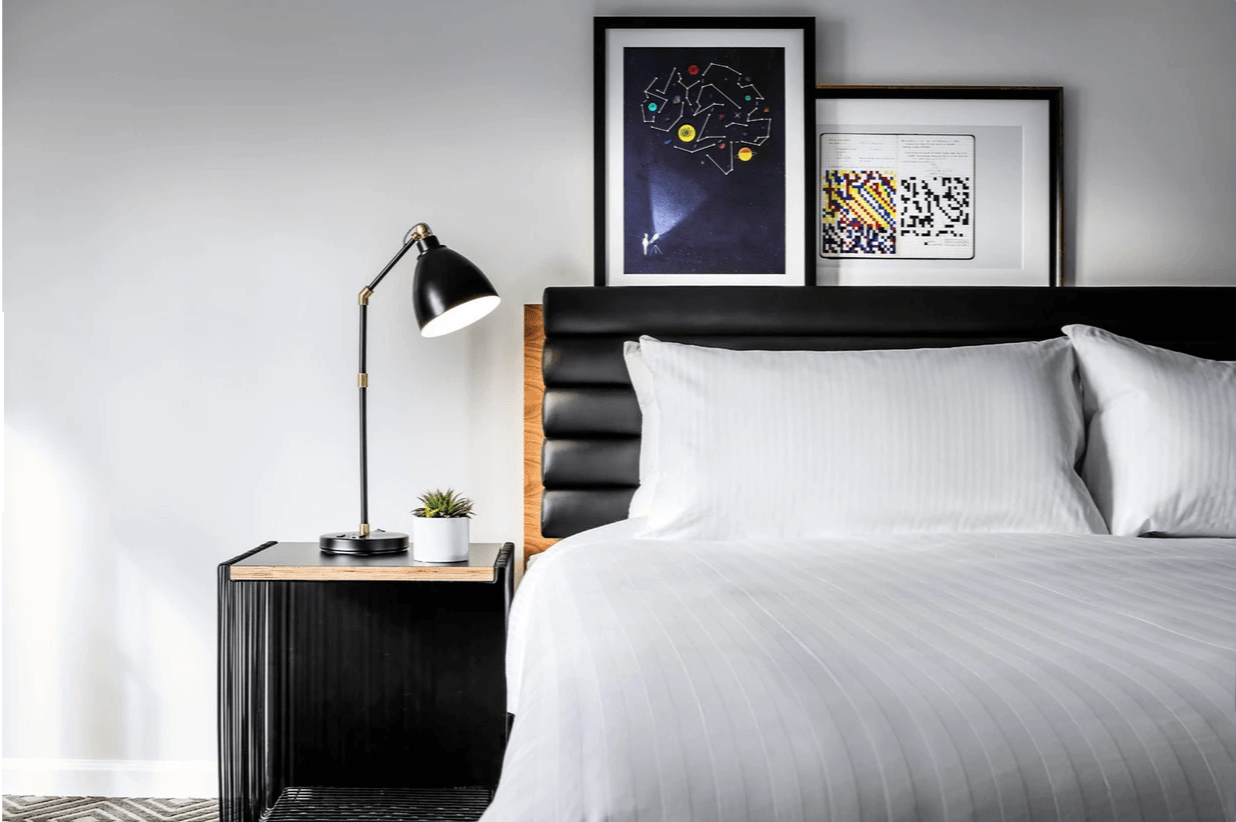
Our Philosophy
Indon operates under parent company, As Specified, Inc, reaffirming owner Rick Gursky’s core philosophy of pricing and producing projects strictly as intended, adhering to the styling details of the professional specifier. “God is in the details” applied to Mis van der Rohe regarding architecture in the middle part of the last century. At Indon, we embrace the same notion. The small design details are often the easiest to forget. But it’s those small things, tiny minutia of detail, that ultimately make beautiful products that make a design come alive. We do not cut corners
But the logistics and the finances in the world of the Hospitality Industry matter just as much. That is why the very experienced staff at Indon will always clearly identify any potential cost savings as a separate, highlighted line item and alert clients to potential issues in durability, transportation, or installation of the specified pieces
Scope of Products
Indon is committed to servicing the Hospitality Industry. Every manufacturer wants the large quantity, easy to produce projects and they often refuse the smaller, more complex needs of the project. We believe this is a disingenuous approach to servicing the industry. We listen to our clients and their vision’s needs and are always ready to help. Good things rarely come easy. Whether its smaller quantity seating or case goods for Presidential Suites and Lobbies, or a new concept barn door or closet system, we are always willing to go to work for the project and do our homework to successfully execute the vision or need.
About Indon
Over the past 23 years, Indon International has specialized in the manufacturing of custom casegoods and seating for 3 to 5-star hospitality projects worldwide. Having worked with designers, owners and purchasing companies on over 1900 projects with 1.4 million plus custom pieces produced, we certainly understand the intricacies required to manufacture products that not only have a beautiful design aesthetic but are also functional and cost effective.
While a great majority of our products were created for guestrooms, we also produce items for public areas and restaurants as well. Having worked with virtually every major hotel brand in the industry including Marriott, Hilton, Intercontinental Hotels, Westin, Four Seasons, Waldorf Astoria and Embassy Suites - among many others, we understand the need for exceptional craftsmanship. Manufacturing capabilities in the US, North America and overseas also allow us the flexibility to handle virtually any project requirement clients may have.
We understand you have a choice of vendors to utilize. Collaborating with Indon will provide you with a partner who possesses an impeccable reputation for integrity and ethics along with a dedicated, professional and proactive support team. All of this will work together to ensure that your project is completed on time with a quality of product that exceeds your expectations.
We look forward to the opportunity to make your next project a rousing success!
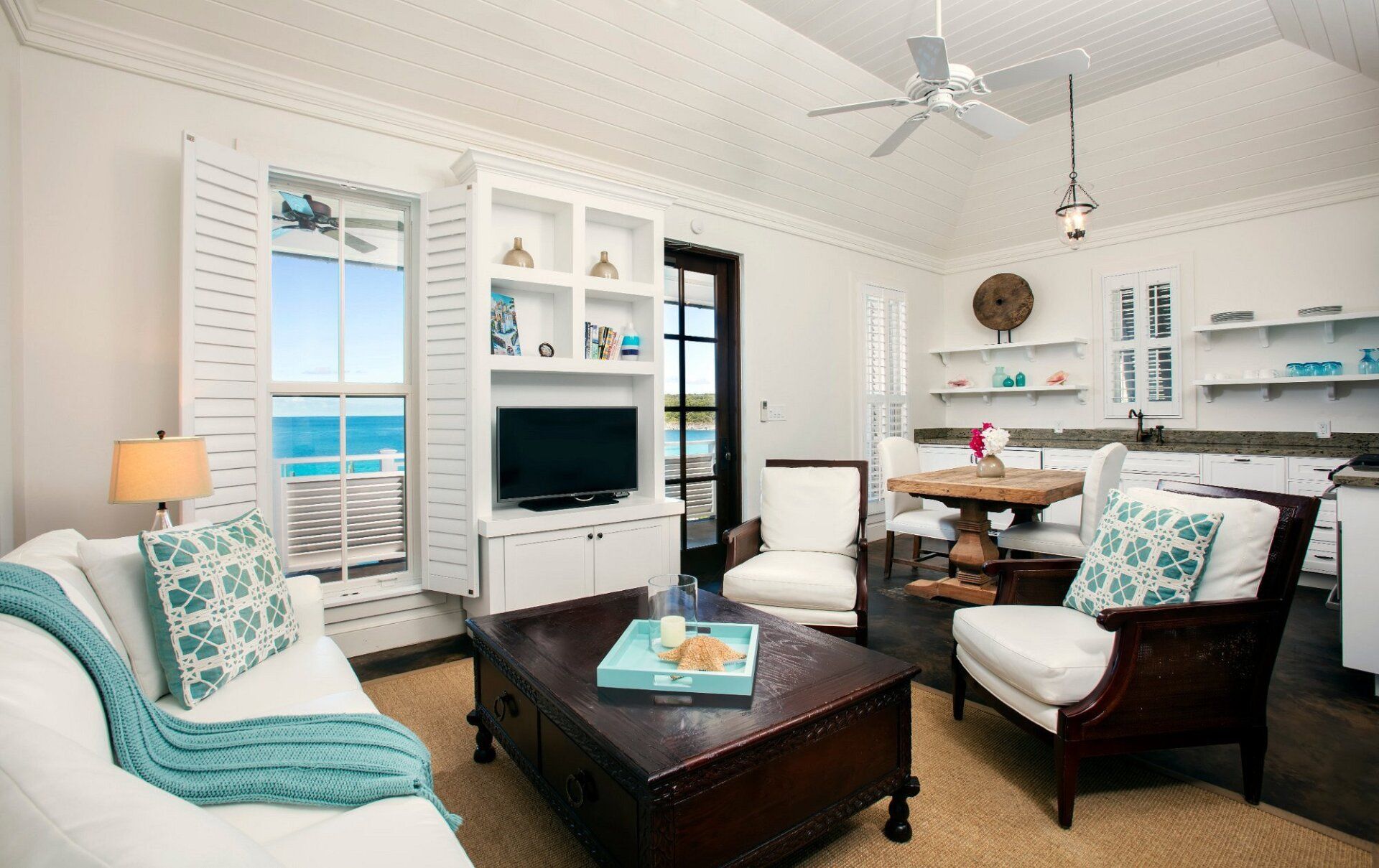
Our Process
Communication
As a new order is entered into our system, you are provided a dedicated Project Manager who will guide you all the way through the process. Weekly updates are proactively sent to advise the current status (shops, finishes, lead times, etc.). Progress photos of production are also available upon request. Shipping information included bills of lading and expected delivery times are tracked and updated until the products arrive at the receiving location.
Custom Design
Having specialized in the manufacturing of custom casegoods and seating for over 20 years, we truly understand the intricacies associated with creating product that has never been made before. Taking a design concept from idea to reality is truly a specialized art form. Maintaining the design aesthetic desired while ensuring functionality and all the while keeping a product cost effective has been our forte’ since the company’s inception.
Starting with a design concept and inspiration images, we can guide clients through all aspects of a product’s construction. We work with a wide variety of base materials such as solid wood, veneers, high pressure laminates, metal, stone, glass and resin to bring these designs to life.
Initial review
Once specifications are received, we will examine the concept and make initial recommendations related to any areas of concern. We will also provide value engineered recommendations for consideration.
Shop Drawing Process
Following the initial review, we will create CADS for revaluation and approval. In this stage, the attention to detail is of paramount importance and as such, these must be reviewed very carefully.
Finish Approval
While we have many standard finishes to choose from, we can also match custom finishes. Simply provide us with the desired finish and in a matter of a week or so, we will send back options for approval. Over the years, clients have raved about the quality of our finishes as one of the aspects that truly sets us apart.
Production
Once all approvals are in place, we move to the manufacturing stage. Depending on where your products are being produced and the size of the project, lead times are typically 8-10 week after all approvals for US and Mexico production and 12-14 weeks for overseas production (to a US Port).
Post shipment
Where appropriate and warranted, we will send a factory representative to be on site for the start of project installation. Following proper techniques and protocols is crucial in many installations and getting the project started on the right track can minimize unforeseen challenges down the road. Our team always remains constantly available for consultation throughout the process with follow-up calls being made to ensure everyone is pleased with the outcome of the installation
We pride ourselves on the impeccable ethics and integrity with which we operate day in and day out. Our goal is your complete satisfaction!
Manufacturing
With manufacturing capabilities in the US, Mexico and overseas, we have the flexibility to meet just about any project requirement you may have. From large quantity guestrooms to public areas and restaurants, we are willing to accept just about any need you have for seating or casegoods for your hospitality projects. Each factory follows strict guidelines and utilizes state-of-the-art equipment, technology and techniques which allow us to create the most intricate of custom pieces for 3 to 5 star hospitality projects. Long term partnerships, an impeccable attention to detail and on-site quality control by our employees enable us to serve our clients in the manner with which they expect and deserve.
Seating/Upholstery
We produce all types of fully or partially upholstered seating with exposed metal and wood including lounge chairs, sofas, recliners, banquettes and sleeper sofas as well as desk chairs, dining chairs, barstools, luggage benches. In many cases, we will go ahead and put product into production with a firm commitment for COM delivery. This is extremely helpful as many times fabric requires longer lead times and this commitment allows a project to remain on track.
Casegoods
We produce virtually every type of case good product imaginable. Everything from headboards with integrated connectivity, nightstands, credenzas, dressers, dining tables, entertainment centers and vanities for guestrooms to consoles, cocktail tables, side tables, buffets and see tables for public areas can be custom designed and built to your specifications.
Indon has curated a list of high quality partner factories throughout Asia, Mexico, the Caribbean and Central and South America.